I. Production range

II. Productivity
4 pcs/min, 2 shifts/day, 260 working days/year.
Productivity per year 4×60×2×8×260=998,400 pcs
III. Production flow chart
IV. Key equipment description
1. CNC disk saw
CNC disk saw is used to cut off steel billet efficiently and accurately. Steel billet cut by CNC disk saw has nearly no section slope, which is very suitable for further forming process, especially the coal pick is formed vertically. Steel billet cut by CNC disk saw has very little weight error, which is the guarantee of closed die forging without flash. The working efficiency of CNC disk saw is 5 times of traditional band saw. One operator can operate 4 sets of CNC disk saw without any problem, with less labor cost.
2. Automatic intermediate frequency induction furnace
Automatic intermediate frequency induction furnace is used to heat steel billet to required forging temperature. This induction furnace is equipped with automatic step loader, the operator only need to put steel billets into step loader in bulk. The automatic step loader raise the steel billet horizontally to the feeding channel, the chain or pneumatic feeding rod will push the steel billet into the induction coil. Inside the induction coil, the steel billet is heated to required forging temperature.
The induction furnace is equipped with infrared thermometer to detect the steel billet temperature. Closed type cooling tower is adopted to cool down both induction coil and intermediate frequency power source.
3. Forging press
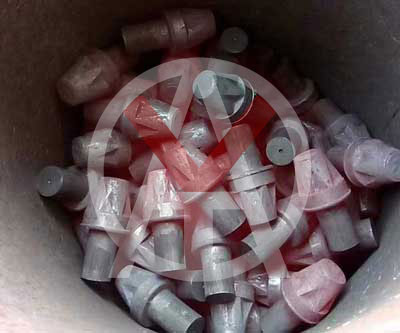
Forging press is used to form the basic shape of coal pick. In order to decrease oxide coating and improve the surface quality, warm forging is applied in this process. The stroke is long enough for coal pick forming.
Not only forging press, but also forging dies and graphite spray station can be supplied together.
4. CNC lathe

CNC lathe is used to machining the surface of coal pick to satisfy the installation precision requirement. The CNC lathe adopts sturdy and serviceable horizontal flat bed. The bed foot is an integral box structure, which is casted by high standard cast iron (HT300) in one time and has good stability through secondary aging treatment. The spindle box has high rigidity and can adapt to the heavy cutting processing. Each sliding guide rail pair is covered with TSF soft belt, which greatly reduces the friction coefficient and improves the servo response performance. The precision ball screw pair is used in the X-axis and Z-axis to ensure high machining accuracy, positioning accuracy and accuracy retention. The tailstock has sturdy structure to withstand heavy cutting and fix coal pick.
5. Automatic induction brazing and quenching machine
Automatic induction brazing and quenching machine is used to braze coal pick frame and cemented carbide head together, and the remaining heat of coal pick after brazing is used to quench coal pick to achieve required hardness.
The automatic induction brazing and quenching machine is equipped with conveyor made of heat resistant stainless steel. Coal picks are place on the stands on conveyor, the conveyor will forward the coal picks into induction coil to heat them to required brazing temperature. The pressing rod of automatic induction brazing and quenching machine will press down the carbide head to release gas during brazing process, in this way, brazing quality can be ensured.
After brazing, the coal pick still has remaining heat, which is more than enough for quenching. Then the conveyor moves the coal picks forward for some distance until the temperature drops to quenching temperature. Then the temperature is just right for quenching and directed by infrared thermometer, the PLC controls manipulator to remove coal picks from stands, and put them into quenching pool. After the quenching process is finished, the coal picks are gotten out of quenching pool by another conveyor.
The whole processes above are fully automatic, the operator only needs to put coal pick to stands on conveyor stand, greatly decreasing labor cost.